Health and Safety Job in Nigeria; Starting and growing a career in HSE.
TABLE OF CONTENT.
- Preparing to get into the health and safety profession.
- Safety officer variations
- Health and Safety Organization
- Why is it important to become an ISPON member?
- Other Safety organizations
- Health and safety training firms in Nigeria
- Which education level do you need to join the profession
- Safety roles and responsibilities as seen on Job adverts.
- ISO management system standards
- Qualities of a health and safety professional
- Duties and responsibilities of a health and safety officer.
- Some Health and Safety terms you should be familiar with.
- Volunteering to work for free.
- Volunteering to teach for free.
- The things health and safety officer should be doing at work.
- Few health and safety blogs you should follow.
- Organizations where a health and safety officer can be employed.
- Laws and regulations affecting health and safety in Nigeria.
- Personal protective equipment.
- Emergency response team.
- Security and Access control in the workplace.
- Good housekeeping.
- Conclusion.
- Reference.
PREPARING TO GET INTO THE HEALTH AND SAFETY PROFESSION.
The first thing to know before going into the health and safety profession is for you to know the meaning of the health and safety profession.
Most of the people I have met found it very difficult to even know what it is all about. Some people will tell you that they’ve never heard it before.
Well, the health and safety profession is not new again, and it has come to stay in the world and Nigeria inclusive.
Health and safety have been established as far back as 1950 by the World Health Organization. But then, in the UK, when we had the Piper Alpha rig incident in July 1988, a lot changed in the health and safety approach in the workplace.
That incident claimed the lives of 165 crew members out of 226 crew members and 2 crew members from the standby vessel Sandhaven and destroyed properties worth billions of dollars.
The incident is regarded as the worst offshore oil disaster in the history of the UK.
In the United States, OSHA (Occupational Health and Safety Administration) was officially established on April 28, 1971, as the federal body responsible for worker health and safety.
Currently in Nigeria, the awareness of health and safety is gradually gaining ground but we are not yet there even though we have so many bodies on the front line for it for a very long time now.
LET’S KNOW WHAT “HEALTH” and “SAFETY” MEANS.
Health means the absence of disease or ill health. Health relates not only to physical health or ill health but also to psychological health or ill health.
Safety is the absence of risk of serious personal injury.
It is the state of being “safe” (from Frech sauf), the condition of being protected against physical, social, spiritual, financial, political, emotional, occupational, psychological, educational or other types or consequences of failure, damage, error, accident, harm or any other event which could be considered non-desirable.
Safety can also be defined to be the control of recognized hazards to achieve an acceptable level of risk. It can include the protection of people or possessions.
SAFETY OFFICER VARIATIONS.
Safety officer has a lot of variants depending on what the company wants to achieve or what they want in their organization. In some companies, the safety officer has no other role apart from safety. And can be called a Safety Officer.
In the profession, we are all called OSH PROFESSIONALS-Occupational health and safety professionals.
In some companies they are called, Health and Safety Officers or Health, Safety and Environment (HSE) officers. Others use Environment, Health and Safety officers (EHS),
You can also see QHSE Officers; in this case, the department is combining quality with health, safety and environment.
You can also see the QHSSE Officer; In this case, we have the quality, health, safety, security and environment together.
We have these variations depending on the company’s needs at that time. I’ve seen many job adverts carrying this variation, they are telling you to know what you should expect in the line of the job. So you’ve to prepare along that line.
In some companies, they may have an environment officer separately apart from the safety officer. They may have a trained nurse with qualifications in Health and Safety to fit into the role of a health and safety officer.
So if you’re a nurse, you already have an upper hand in getting the job more than anyone else who is not health personnel in that establishment.
Some companies do hire first aiders who solely do first aid jobs for them.
SAFETY ORGANISATION IN NIGERIA.
There are so many safety organizations in Nigeria, for example, NISCN- National Industrial Safety Council of Nigeria, ISPON, etc. but ISPON has been at the forefront and it was enacted by an act of the Parliament of Nigeria as a chartered institute body.
ISPON is an acronym for the Institute of Safety Professionals of Nigeria. It became a chartered body in 2014.
For someone who wants to join a safety profession, ISPON should be your first start.
As an Institute, ISPON offers training on Health and Safety every month in all their centres across Nigeria.
There are also rooms for someone to become a member and progress along that line to become a Fellow of the Institute and this is the highest membership grade.
If you’re a university or polytechnic graduate, for you to join ISPON, you’ve to show evidence of certificate that you’ve undergone General Health, Safety and Environment training conducted by ISPON. Also, HSE level 3 training was conducted by ISPON.
These two certificates are the first requirements to apply for membership in ISPON.
From there, you can pay for the membership fees, Exam/Interview fees, and the induction ceremony fees for you to join.
WHY IS IT IMPORTANT TO BECOME AN ISPON MEMBER?
Most job adverts in Nigeria for the health and safety profession have it in their requirement for you to even submit your CV to them.
There are some companies you can’t practice as a Health and Safety Officer if you’re not a member of ISPON.
ISPON Chapters have monthly meetings where members meet. They usually have technical sessions where people can learn and improve on their Continuous Professional Development.
In this profession, if you want to succeed very fast, you need to keep on learning. Learning is limitless in the health and safety profession. There are so many things to learn. So many books to read. So many courses to do. And being a member of ISPON will give you a first step and an overview of that aspect.
ISPON maintains a register of members in their various chapters that they can refer to or recommend you for jobs when you’re registered with them.
In my ISPON chapter, I hardly miss monthly meetings, because it’s very beneficial to me.
We’ve members from other professions with whom you can interact and network and share work experiences on Health and Safety together.
For example, we have engineers, doctors, architects, builders, accountants, Military personnel, etc. in our chapter.
OTHER INTERNATIONAL SAFETY ORGANISATIONS.
There are other International Safety Organizations, and some have good visibility in Nigeria such as
WSO (World Safety Organization),
IOSH (Institute of Occupational Safety and Health),
International Institute of Risk and safety management (IIRSM),
ASSP- American society of safety professionals,
CSSE- Canadian Society of safety engineering,
CCOHS-Canadian Centre for Occupational Health and Safety.
BCSP- Board of Certified Safety Professionals.
Board of Canadian registered safety professionals etc.
You can become their member by paying certain amounts of fees with scanned copies of your credentials to them for review, but I’ll encourage you to concentrate more on ISPON while you progress to join others later. `
IOSH Is a UK organization. Everyone joins IOSH as an affiliate member. You can now pay for full membership, and they’ll upgrade you depending on your CV, and the certificate you’ve.
If you’ve got a NEBOSH NGC/IGC Certificate, they’ll grade you as a technical member of IOSH(Techiosh) and if you have a NEBOSH diploma certificate, they’ll grade you as a graduate member of IOSH (GRADIOSH).
Though there are other routes you can follow to join any grade in IOSH. If you find it difficult, you can always communicate with IOSH for guidance on how to go about it.
IOSH West Africa has its informal meetings depending on your location in Nigeria.
Most Job adverts from the UK and some multinational Jobs will require you to be a member of IOSH or any of the International Safety Organizations when submitting a CV to them.
But don’t worry, take it gradually.
IOSH will require you to be paying yearly dues which may be taking much from you as a beginner in the profession.
IOSH has courses someone can do; the two popular ones are working safely and managing safely.
If you have the money, you can give it a try but if you don’t have, you can save up to get any of them.
NEBOSH IGC- Nebosh International General Certificate.
NEBOSH is an examination body that organizes health and safety examinations only. NEBOSH is the National Examination Board for occupational health and safety. They are a reputable charity organization in the UK, They have a range of courses people can sit for through NEBOSH Course providers /accredited centres.
And the exams would be conducted in the British Council. NEBOSH IGC is done online now because of the COVID-19 pandemic issues.
NEBOSH Examinations are easy to pass if you read very well before sitting for the exam. It’s always good for a practising health and safety officer to sit for any of the NEBOSH examinations because some questions are technical and will require an experienced person in the field to answer them correctly.
HEALTH AND SAFETY TRAINING FIRMS IN NIGERIA.
We have many HSE training firms in Nigeria in most of the main cities of the country. Few of them are
1. Safeguard resources ltd- Port Harcourt.
4. Novelle Center.
They have authorized training centres for NEBOSH, IOSH and ISPON and they’ve other bespoke courses depending on individual and company demands.
If you’re finding it very difficult to choose a training firm, you can email me at info@validworth.com or onyekachiemmanuel@gmail.com, and I will guide you on the best training firm to use.
Validworth is partnering with some of the firms to ensure that we give our students the best learning experience for them to excel greatly in their examinations.
WHAT EDUCATION LEVEL DO YOU NEED TO JOIN THE PROFESSION?
For someone to practice HSE in Nigeria you need a Bachelor of Science B.Sc. or HND degree certificate either in science, or in engineering, and fewer of those in management or arts, because most job adverts always carry science or engineering background.
But if you’re not in this category, don’t lose hope. You can still get a job as a health and safety officer if you apply most of the things in this book.
You could be picked during an interview depending on your delivery and composure and on the health and safety certifications that you have done.
SAFETY ROLES AND RESPONSIBILITIES FROM A PARTICULAR JOB AS ADVERTISED ONLINE.
Like most jobs, Safety jobs also come with roles and responsibilities that an intending employee should be familiar with when submitting the Curriculum Vitae. Please make sure you’re familiar with it.
Below are the likely roles and responsibilities you’ll see in a job advert. Let’s take a look at the example below as seen on an advertised job from a company called Pirotti Project Limited.
Health, Safety and Environment (HSE) Officer
Pirotti Project Limited
Abuja (+1 other)
Apply on Jobs In Nigeria | Mrjobsnaija
Full–time
HSE Officer
Job Description: HSE officers, also known as health, safety, and environment officers and environmental health and safety officers, monitor health and safety, assess risk, and design strategies to reduce potential hazards within an assigned workplace or geographic area. Private companies and government offices hire HSE officers to work full daytime weekday hours, both in-office environments and out in the field. HSE officers manage and train other health and safety staff members and may even travel to perform field investigations and respond to incident reports. DUTIES INCLUDE: • Ensure adherence and compliance with all relevant legal rules and regulations. • Educate and oversee employees on health and safety procedures and regulations. • Develop and implement health, safety and environment policy and procedures for the company. • Monitor personnel and workspace to ensure the environment is healthy and safe. • Always ensure the company is prepared to submit all the relevant health and safety documents. • Encourage and promote the use of safer work equipment, PPE, materials and supplies in the construction site, and ensure that non-compliant staff are reported to Human Resources. • Ensure that all visitors, vendors and contractors entering the construction site have on their PPE and restricted access without it. • Track the number of incidents and produce reports. • Monitor exposure to certain hazardous materials, etc. • Attend meetings with other managers and Heads of Departments to give and receive update briefs concerning HSE matters and policies. REQUIREMENTS: • Previous working experience as Environmental Health and Safety Coordinator for x years • Certification in Environmental Health or Related Fields e.g. HSE I, II, III • In-depth knowledge of Health, Safety and/or Environmental policy for Construction Sites. • Hands-on experience with performing audits and writing reports. • Excellent organizational time-management skills. • Great interpersonal and communication skills. • Strong personality, proactive and very energetic. • Must be able to work long hours.
ISO MANAGEMENT SYSTEM STANDARD.
Every health and safety professional must be familiar with these three ISO management system standards.
The three standards are ISO 9001:2015, ISO 14001: 2015 and ISO 45001:2018.
ISO which is called International Organization for Standardization has a network of national standard bodies and has more than thirty-eight thousand standards currently.
Knowledge of the standards will help you to understand what you’re expected to do when you find yourself in an environment that exposes you to an audit process and for you to apply professionalism in your work as expected.
When you apply, appreciate and know how to implement the standards in your work, your work will be more professional and you will know the reasons to follow procedures very carefully at work.
It’ll also help you to value the importance of HSE documentation and make you not see it as a mere formality in your company.
These three standards are very important. I want you to take some of your time to study them the more. If you can understand the standard as a health and safety professional, most of your job will be easy for you.
In this profession, we keep a lot of documents for reference and auditing purposes.
Even if you’re working in a place where the management doesn’t subscribe to any of these standards, you can use them in your day-to-day work to improve your delivery and equally prepare yourself for better opportunities elsewhere.
Standard is a just formula that describes the best way people can do things. It could be about anything such as making a product or rendering a service.
For example, the environmental management standard helps to reduce environmental impacts and waste and provides sustainability.
ISO standards are not meant to be a legally binding document for companies that subscribes to them but it’s just a management tool that organization can use voluntarily on their own.
These three standards listed above are closely related to each other because they follow the Annex L structure.
Annex L is a section of the ISO/IEC Directives part 1 that prescribes how management system standards should be written.
Before 2012, every ISO management system standard was written differently, now, they’ll have the same structure courtesy of Annex L.
It contains ten clauses in the arrangement thereby allowing for easy integration when you’re combining any of the standards with each other.
Please find below the Annex L structure for every management system standard.
- Scope.
- Normative reference.
- Terms and definitions
- Context of the organization.
- Leadership.
- Planning
- Support
- Operation.
- Performance evaluation
- Improvement.
QUALITY MANAGEMENT SYSTEM –ISO 9001-2015.
ISO 9001:2015 requirement is the only standard in the ISO 9000 family series to which organizations can get certified. Other standards in the series are
ISO 9000:2015-fundamentals and vocabulary (definitions),
ISO 9004:2018 quality management-quality of organization guidance to achieve sustained success (continuous improvement),
and ISO 19011:2018-guidelines for auditing management systems.
ISO 9001:2015 standard came into being in 2015. Since then, it has been widely used by companies and organizations to improve quality and customer satisfaction in their workplace.
According to ISO, more than one million organizations from more than 170 countries of the world have applied the requirements of the standard to manage their quality management systems.
So the implementation has helped them to organize their processes, remain in business, retain their customers and bring about greater efficiency in the management of resources within the organization.
Just like every other management system standard, QMS ISO 9001:2015 is based on the PLAN-DO-CHECK-ACT methodology which can be called the Demin cycle.
It provides a process-oriented approach to the management of the system. Also the requirements of the standard are generic and can be applied to any organization regardless of the size, products, or services it provides.
ENVIRONMENTAL MANAGEMENT SYSTEM ISO 14001:2015.
This standard was developed in the year 2015 specifically to cater to environmental issues holistically. It’s standard in the family of ISO 14000 that organizations can be certified to.
Other standards in the family are ISO 14000:2016- general guidelines on implementation and ISO 14005:2019- guidelines for a flexible approach to phased implementation.
According to ISO, there are over 300000 certifications to ISO 14001 in 171 countries around the world. An organization can use it to enhance their environmental performance.
It is suitable for organizations of all types and sizes and its factors in environmental issues relevant to the organization’s operations. Issues like
- Air pollutants
- sewage issues,
- soil contaminations
- Air emissions
- Releases to land
- Releases to water
- Raw material and natural resource use
- Energy uses
- Energy emissions such as radiation, heat, or vibrations
- By-products and waste.
- The environment is affected by the physical characteristics of the company.
Organizations subscribing to the standard in the management of their environment in the workplace enjoys many benefits. The benefits are
It increases leadership in the organization and encourages worker participation in environmental activities.
It improves the company’s reputation and ensures they continue in business for a very long time.
Reduces cost and increases efficiency in the overall operations of the company this, in turn, gives the company a financial advantage over competitors in the market.
The suppliers being integrated into the management process encourages better environmental performance.
It demonstrates compliance with current and future regulatory requirements.
OCCUPATIONAL HEALTH AND SAFETY MANAGEMENT SYSTEM ISO 45001: 2018.
This standard came into existence in 2018. But before it was drafted and adopted, OHSAS 18001 was in use.
In developing the ISO 45001:2018, great consideration was given to OSHAS 18001, International Labour Organization ILO-OSH guidelines and International Labour Standards and conventions-(ILS).
The standard is process-based, unlike what we have in OHSAS 18001, which is procedure-based. The standard considers both risk and opportunities, unlike OHSAS which considers the only risk.
Every day, in our workplaces, workers’ lives are lost due to incidences and illnesses linked to work activities. These are deaths that could have been prevented if the necessary precautions and measures are put in place.
ISO 45001:2018 aims to help organizations put the measures in place and prevent these fatalities.
However, the benefit of ISO 45001 is endless but an organization has to implement it correctly for it to work for them.
When the standard is correctly implemented, it will help an organization to provide a healthy and safer workplace for their workers and for other people who may be affected by their activities.
And it helps prevent deaths and work-related illnesses and diseases and it will continually improve the organization’s occupational health and safety performance.
All these benefits can put the organization’s reputation in good light as a safe place to work, with other associating benefits of reduction in insurance costs and an increase in staff morale. All these make the company fulfil its set occupational health and safety Objectives.
Any health and safety professional who wants to excel greatly must be knowledgeable in these three ISO management standards.
Having only the knowledge is never enough, you need to have the skills on how to apply and implement it in your company. In that case, it can be said that you’re competent.
The knowledge can help you if you want to progress in your career as a management system auditor depending on any of the schemes you want which could be on ISO 9001:2015, or on ISO 14001:2015 OR ISO 45001:2018.
This will contribute to a huge success in your work and ensure that the quality, environmental and occupational health and safety affairs at the workplace are in good shape.
DOCUMENTS A HEALTH AND SAFETY OFFICER or an ORGANISATION NEED TO MAINTAIN AND RETAIN ACCORDING TO THE REQUIREMENTS OF ISO 45001:2018
When you’re employed to start work as a health and safety, you should be able to know the forms and the checklist you’ll be making use of during your work.
If you’re with a company that is following the requirements of ISO 45001:2018, they’ll have documents and forms for you to work with according to the requirements of the standard.
Below is the list of mandatory documents and records to be maintained and to be retained according to ISO45001:2018.
MANDATORY DOCUMENTS ARE
• Scope of the Occupational Health and safety (OH&S) management system. (clause 4.3)
• Occupational health and safety (OH&S) policy. (clause 5.2)
• Responsibilities and authorities within the Occupational Health and Safety Management (OH&SMS) system. (clause 5.3)
• Occupational health and safety (OH&S) process for addressing risks and opportunities. (clause 6.1.1)
• Methodology and criteria for the assessment of Occupational Health and Safety (OH&S) risks. (clause 6.1.2.2)
• Occupational Health and Safety (OH&S) objectives and plans for achieving them. (clause 6.2.2)
• Emergency preparedness and response process. (clause 8.2)
MANDATORY RECORDS ARE
• OH&S risks and opportunities and actions for addressing them (clause 6.1.1)
• Legal and other requirements (clause 6.1.3)
• Evidence of competence (clause 7.2)
• Evidence of communications (clause 7.4.1)
• Plans for responding to potential emergencies (clause 8.2)
• Results on monitoring, measurements, analysis and performance evaluation (clause 9.1.1)
• Maintenance, calibration or verification of monitoring equipment (clause 9.1.1)
• Compliance evaluation results (clause 9.1.2)
• Internal audit program (clause 9.2.2)
• Internal audit report (clause 9.2.2)
• Results of management review (clause 9.3)
• Nature of incidents or nonconformities and any subsequent action taken (clause 10.2)
• Results of any action and corrective action, including their effectiveness (clause 10.2)
• Evidence of the results of continual improvement (clause 10.3)
NON-MANDATORY DOCUMENTS.
• Procedure for Determining the Context of the Organization and Interested Parties. (clause 4.1)
• Occupational Health and Safety (OH&S) Manual. (clause 4)
• Procedure for Consultation and Participation of Workers. (clause 5.4)
• Procedure for Hazard Identification and Assessment. (clause 6.1.2.1)
• Procedure for Identification of Legal Requirements. (clause 6.1.3)
• Procedure for Communication (clause 7.4.1)
• Procedure for Document and Record Control (clause 7.5)
• Procedure for Operational Planning and Control. (clause 8.1)
• Procedure for Change Management. (clause 8.1.3)
• Procedure for Monitoring, Measuring and Analysis. (clause 9.1.1)
• Procedure for Compliance Evaluation. (clause 9.1.2)
• Procedure for Internal Audit. (clause 9.2)
• Procedure for Management Review. (clause 9.3)
• Procedure for Incident Investigation. (clause 10.1)
• Procedure for Management of Nonconformities and Corrective Actions. (clause 10.1)
• Procedure for Continual Improvement. (clause 10.3)
QUALITIES OF A HEALTH AND SAFETY PROFESSIONAL.
As a safety professional, you’ve to build yourself around these qualities while discharging your duties in the workplace.
- Ability to demonstrate genuine concern for others.
- Respect for your team and
- Having an ability to reward good behaviour.
- Good planner
- Timely responsive behaviour.
- Being proactive at all times
- Strong communication
- Strong sense of responsibility
- Hungry for knowledge
- Showing leadership by example
- Result-oriented at all times
- Showing humility and a sense of purpose.
DUTIES AND RESPONSIBILITIES OF A HEALTH AND SAFETY OFFICER.
- Auditing production, keeping on the lookout for any unsafe behaviour or breaks in regulations
- Assessing risk and possible safety hazards of all aspects of operations
- Creating analytical reports of safety data
- Inspecting production equipment and processes to make sure they are safe
- Ordering repairs for unsafe and/or damaged equipment
- Focusing on prevention by keeping up with equipment maintenance and employee training
- Presenting safety principles to staff in meetings or lecture-type training sessions
- Participating in continuing education to update knowledge of health and safety protocols and techniques
- Determining whether the finished product is safe for customers
- Creating safety plans that include suggested improvements to existing infrastructure and business processes
- Sharing information, suggestions, and observations with project leadership to create consistency in safety standards throughout the production team and the entire company
- Meeting company health and safety goals
- Investigating the causes of accidents and other unsafe conditions on the job site
- Liaising with law enforcement and other investigators who are present at the time of a serious accident
- Finding the best way to prevent future accidents
- Reviewing and reporting on the staff’s compliance with health and safety rules and recommending commendations or dismissal based on performance
From – Monster.co.uk
KEY TERMS AND DEFINITIONS, YOU SHOULD BE FAMILIAR WITH THE PROFESSION.
HAZARD– Something with the potential to cause harm.
RISK– the likelihood that a hazard will cause harm in combination with the severity of the injury, damage or loss that might occur.
POLICY– Intentions and direction of an organization as formally expressed by its top management.
SAFETY – the absence of risk of serious personal injury
WELFARE– access to basic facilities
WORKPLACE– A place under the control of the organization where a person needs to be or to go because of work.
ENVIRONMENTAL PROTECTION- the prevention of damage to the air, land, water and living creatures in the wider environment.
INCIDENT- Work-related event in which an injury, ill health or fatality or damage occurred or could have occurred. Therefore, an incident can be a near miss or an accident.
NEAR MISS- an unplanned, unwanted event that had the potential to lead to injury, damage or loss but did not do so
ACCIDENT- an unplanned, unwanted, event that leads to injury, damage or loss.
COMMUTING ACCIDENT– An accident to a worker that occurs when they are travelling to and fro from their workplace, the place where they take a meal during working hours, or the place where they collect their pay.
DANGEROUS OCCURRENCE– A specified event that has to be reported to the relevant authority by statute law.
WORK-RELATED ILL HEALTH-diseases or medical conditions caused by a person’s work.
VOLUNTEERING TO WORK FOR FREE.
Please take this part very seriously. This is where the main thing is. And you must take it seriously.
Even when you’ve done all you could do to get a job and the job is not forthcoming.
The fastest way to get work is to locate an HSE training firm near your location and volunteer to work for them for free. However, some companies may decide to be giving you stipends for your transport fare depending on the generosity of the management.
This does not just work for HSE jobs but in all jobs, if someone wants to get work very fast.
When working in those places, will expose you to many candidates coming in for training from various companies.
From there, you can connect with them and ask them for referrals in their companies when there is an opening.
We all know that most jobs are not advertised now, they are mostly filled by word of mouth, and networking with people coming in for training where you’re working for free will help you to get a job very fast.
Always ensure that you establish contacts with them, build a relationship, and also memorably present yourself to them at all times. Sure you are likely to be lucky someday.
Because you have the experience and knowledge of working in an HSE training firm, it’ll be easy for you to pass through any job interview that you go to.
Most likely training firms that can take you as a volunteer are the ones you have done one or two training with. That is why it’s very important to pay attention when you register for training in any firm. Make sure you read and pass their course very well. It could help you to get a volunteer from there.
A friend of mine did an ISO 45001:2018 training with a firm that I know, the owner of the firm had to beg her to work for them due to her performance during the training.
So if you save some cash try and register for training in a nearby training centre.
You can choose any of their affordable courses and get in first. Be serious about it. Luck may smile on you if you do.
VOLUNTEER TO TEACH FOR FREE TRAINING OR GIVE SAFETY TALKS FOR YOUR COMMUNITY.
Your community is the people around you. Your family, your kindred or your church members or in your mosques. Ask for an opportunity to educate people on any of the safety topics.
You never can tell what’ll happen to you while doing this.
When someone teaches what they’ve learnt or what they’ve known, the topics will register very well with them and over time, it builds them to become leaders in the topics.
There are so many topics in health and safety people can easily teach people.
For example, you can pick up topics such as how to use a portable fire extinguisher, how to fight a fire using a portable fire extinguisher or how to drive safely on the road.
During one of the programs that I attended on a given Saturday, I met a lady who does child and school safety programs.
She develops herself in that particular niche and she is doing very well. She gets the attention of many schools; both private and public schools through free training and most times, the schools invite her for paid delivery.
One thing about volunteering to speak is that it’ll build your confidence and make you a safety leader and if you’re starting new, it’ll help you to command authority in that field within the shortest possible time.
THE THINGS A HEALTH AND SAFETY OFFICER WILL BE DOING AT WORK.
- Induction of all personnel assessing the site.
When a worker is hired, the health and safety officer must conduct a safety induction for the person. There are different types of induction.
There is a common one done at the company’s entrance gate to allow people to gain access to a work site or a factory or plant. However, on employment, a worker has to undergo a detailed safety induction of a workplace.
During the induction, important things such as these are discussed, like the restroom, clinic, places where first aid box is kept, non-smoking area, company health and safety policy, and other policies of the company, Muster point area, various procedures in the company such as emergency procedures, ladder management, Risk assessment, Housekeeping, fire safety.
For the induction done at the gate entrance, in some companies, there are provisions for audiovisuals used in induction, for example, a video is played for the person to see and listen to it.
After that, a written test is conducted to evaluate the person’s knowledge of the induction and the person would be allowed to access the factory has passed the test.
In some places, this is done verbally by the health and safety officer and after that, there is an evaluation of the induction training through writing a test.
No one does work without a permit for that job. Permits are documents that authorize a work to be carried out within a specified time under a safe condition. It’s usually raised by the safety officer but in some companies, they can assign such a role to a Permit officer.
- Inspection of equipment like heavy machines, portable tools, and ladders.
If there are machines such as dumpers, trucks, and forklift trucks used within the site, you’ve to inspect them every morning before use in the presence of the operators or the drivers.
When inspected, if there are safety issues seen, they should be corrected before making use of the equipment.
Inspection forms or checklists are made available for this activity and they are documented after use.
During the inspection, when equipment is bad, the health and safety officer tags it out for repair.
No damage or bad equipment should be on use on site.
- Inspection of vehicles accessing the site.
This one is done at the gate by the security officer or a health and safety officer or any responsible persons that are duly trained and assigned for such a role.
Any evidence of training must be documented and the training must have been from a competent person.
After the inspection, there could be an inspection tag or a duplicate Inspection form given to the driver to serve as evidence of inspection and it could serve as a pass to enable the vehicle to enter the premises.
Things usually checked are the driver’s license, seat belt, brake system of the vehicle, fire extinguisher, the light system
These can be called tailgate meetings or pre-work meetings. It is usually done at the beginning of work in the morning or the beginning of any work shift usually done within 10 minutes.
- Site inspection to make sure that the site is safe for workers.
The health and safety officer has to go around the site environment and inspect the site and put immediate controls against any hazards that might cause harm to workers before they start working for the day. If there are exposed places that can cause harm, the Safety officer can put barriers to prevent workers from accessing such areas with Caution tape or barricades,
This is done monthly, weekly or once in two months on some sites and it is compulsory for everyone on site.
Presently, in my workplace, we do our site health and safety meeting once every month.
The health and safety officer organizes the meeting with the head of the site or workplace which can be an engineer or site manager or any senior management personnel like the director.
The meeting is one of the objectives of fulfilling the health and safety policy of an organization.
It is used to raise the safety awareness of the workforce. The meeting has a typical agenda and it should be like this,
- Opening remark by the most senior person in the organization
- Reading of the last-minute meeting
- Matters arising and Corrections from the last meeting
- Monthly health and safety statistics and incident review.
- Presentation of a topic by an in house person or an invited speaker
- Questions from the topic and any other questions
- Any other business.
- Closing remark.
During the meeting. It should be structured and timed properly. Most companies use less than one hour for their meeting. Workers will also have enough time to ask questions and share their experiences and views regarding health and safety and their welfare
- Updating of safety statistics board
The health and safety office also updates the statistics board. The board is always visible in places where workers can see it and where it can’t be tampered with by rain or extreme weather conditions.
You have to be knowledgeable about this aspect very well. You would be required to carry out investigations and write reports whenever there is an incident at the workplace. You’ve to undergo specific training on how to conduct investigations and get your certificate for it. Some companies allow the health and safety manager to head the accident and incident investigation team.
The most senior and knowledgeable health and safety personnel should be given the role of accident investigation. There should be an incident and accident investigation form to allow for uniform and organized reporting. The health and safety personnel should make reports as soon as possible on any incident on-site and make sure there is an incident learning after the detailed investigation.
- Site safety committee meeting.
This is a meeting specifically for members of the safety committee. Personnel such as a head of department or sections, health and safety officers and workers’ representatives.
It could be done once every month. Things discussed include worker’s health, welfare and safety, Incident or accident scenarios if there are any, Safety statistics and so on.
FEW HEALTH AND SAFETY BLOGS YOU SHOULD FOLLOW.
You’ve to stay current on the safety and health information happening around the world. Being current will help you to remain updated and help you to position yourself very well.
Below is the list of blogs you need to follow.
2. Ehsdb.com
3. Hsewatch.com
4. Sefon.com
12. Safetyrisk.net
14. Reddit.com/r/workplace safety
15. Superiorglove.com/pages/blog
16. Ask-ehs.com/blog
17. Shields.org/blog
INDUSTRIES WHERE A HEALTH AND SAFETY OFFICER CAN BE EMPLOYED.
- Construction industry.
- Hospitality industry e.g hotels.
- Catering and restaurants.
- Hospitals and healthcare
- Banks
- Mining industry.
- Food and beverages
- Liquor
- Oil and gas
- Manufacturing
- Transportation and Logistics
- Schools
- Telecommunication
- Power and Electricity Company
- Fabrication industry
- Mining industry
- Agriculture
SOME LAWS, REGULATIONS AND STANDARD AFFECTING WORKERS and HEALTH AND SAFETY IN NIGERIA.
The few ones we have in Nigeria are
- Labour Act Cap L 1, Laws of the Federation of Nigeria (LFN) 2004.
- Factories Act, Cap 126, LFN, 1990.
- Factories Act, Cap F1, LFN,2004.
- National Fire Safety Code.
- Factories (Registration, Etc Fees) Regulations S.I.5 1991
- Declaration of Industrial Diseases Notice LN 114 1956
- Docks (Safety of Labour) Regulations LN 42 of 1958
- Factories Act Exemption Order LN 82 of 1967
- First Aid Boxes (Prescribed Standards) Order LN 188 of 1958
- Factories (Notification of Dangerous Occurrences) Regulations
- LN 105 of 1961
- Factories (Wood Working Machinery) Regulations LN 189 1958
There are so many regulations, laws and standards guiding health and safety depending on the country. The list is enormous. Click on this link http://www.ilo.org/dyn/legosh/en to see the various lists.
PERSONAL PROTECTIVE EQUIPMENT.
Most workplaces that are safety compliant do not allow workers to enter the plant without wearing the basic PPE such as safety boots and vests. Then when they’ve entered the plant to do their jobs, they can now put on their helmet, hand gloves, goggles, facemasks or respirators and any other type of PPE depending on the nature of the work they want to carry out.
Always know that it is the responsibility of the employer to provide PPE for the employees and the worker’s responsibility to make use of them and to keep them safe after work.
You’ve to ask how your company does the PPE issuance to their staff. Some companies allow their store or inventory officer to handle such responsibility and, in some companies, the health and safety officer does that role.
Some companies have a laid down procedure for PPE Issuance, ensure you ask properly and know what to do.
When a PPE is issued to a worker, the worker registers his name and signs his signature to show the acceptance of the PPE.
PPE is the last line of defence when other control measures in the hierarchy have been considered.
HIERARCHY OF CONTROL.
These are simply the controls being used to reduce the effect of hazards in the workplace. In the control of hazards, it’s always advisable to follow it in the other of the hierarchy by starting with elimination first.
- Elimination– For example, manual handling presents many risks to health and safety, and such can be eliminated by introducing lifting equipment such as hoists and lifts.
- Substitution– This is introduced when elimination can’t be fully utilized, and to achieve this, substituting one hazard with another that creates less risk is introduced. For example, the use of a handling aid to carry materials doesn’t eliminate manual handling risk but it does reduce the risk of injury.
- Engineering method– This involves using an engineering method to control the hazard altogether. For example, the use of interlocking guards on machinery offers protection to the person operating the machine. Such interlocking guards allow the machine to stop when the guard is open and vice versa.
- Administrative method– This involves the control used by the management by introducing and enforcing policies and safe work procedures at the workplace.
- Use of PPE– This is equipment or clothing worn by a worker that protects the worker from one or more risks to health and safety. Although, it’s the last line of defence and it doesn’t eliminate the hazard but reduces the impact of the hazard and offers protection against the hazard.
FIRE EXTINGUISHER.
- You’ve to know the type of fire extinguishers that are in your workplace.
- You have to know how to make a request for the servicing of an extinguisher and know whose job it is to make such a request for the servicing of the fire extinguisher when it is due.
- Inspections should be done daily and monthly to make sure that they are in order.
- Don’t wait for the extinguisher to expire before you plan for the servicing.
- The servicing of the extinguisher should be every 6 months and when used, it should be refilled immediately.
- Also, know the various types of extinguishers readily available in the market for you and those you’ve in your workplace and make sure you use them correctly- we have mostly the DCP and CO2, and their sizes are 1kg, 3kg, 6kg, 9kg, and 50kg. Etc.
- Get knowledge on the various parts of the fire extinguishers such as the strap, nozzle, hose, pin, tie
- Study the fire action plan and Emergency response plan of your company.
- Know how to operate a fire extinguisher when you have one to use;
P- Pull the pin
A-Aim at the base of the fire.
S- Squeeze the lever.
S- Sweep or swipe from side to side.
EMERGENCY RESPONSE TEAM.
- There should be members of the emergency team in your organization
- Mostly in all companies, the health and safety manager is the head of the team or the safety director depending on the structure.
- You can have the security manager, the medical personnel in the clinic as members, and the ambulance driver.
- The presence of an album for the team with their contacts on the notice boards is visible to all in the company.
FIRST AID.
- You’ve to know the locations of the first aid boxes in your workplace
- You’ve to be knowledgeable about first aid and know how to administer it under different conditions of injuries, even when you don’t have that role as a health and safety officer.
- Ensure you carry out your inspection of the first aid box accordingly with a checklist.
- Remove any expired items from the box and make sure you replace them with new ones.
- Some companies do have designated first aiders apart from health and safety officers. Ensure to know the type of arrangement existing in your workplace.
- Ensure you know the sizes of first aid boxes in your workplace and know the quantity that you have.
- Master the contents of the fire extinguisher and how to perform simple first aid on people.
- Likely contents you should have in your first aid box include Cotton wool, plasters, pins, methylated spirits, hydrogen peroxide, a kidney dish, a latex disposable hand glove,
- First aid equipment should be available for example, eyewash stations, stretchers, emergency showers, blankets, and wheelchairs. This will vary depending on the size of the workplace.
SECURITY AND ACCESS CONTROL IN THE WORKPLACE.
There should be a site security and access control procedure to cater for this section. Majorly this affects the security department in the company the most.
The content of such a procedure should be in this manner.
- Security personnel to always close the entrance gate
- The main gate serves as access for anyone coming into the company.
- Workers to access the site with means of identification
- Sign in on arrival and sign out to be for all persons entering the site or the company.
- Visitors logbook for visitors at the security gate.
- Declaring all personal items accessing the site and registering them at the gate.
- The checking of vehicles at the gate before gaining entrance.
- Declaring of all materials and tools at the entrance gate
GOOD HOUSEKEEPING.
This is more like an everyday word in the industry. You need to be familiar with it.
We usually encounter good and bad housekeeping in the workplace.
Housekeeping simply means a place for everything and everything in its proper place.
It also means having general cleanliness and an orderly arrangement of materials and equipment.
Housekeeping has a lot of benefits if it is properly maintained in an organization.
- Good housekeeping eliminates accidents
- It increases production
- It eliminates fire sources and encourages a good working environment.
You also need to encourage other workers to report things that are not in order in the workplace and you take action to address them.
REFERENCE:
Read also:
- How do we make the health and safety policy accessible to all workers
- Knife safety tips you can apply when using a knife
- Knife safety tips you can apply when using a knife
- Transportation safety toolbox talk
- 37 Chemical handling safety tips.
- 30 hand safety tips to prevent hand injury
- What does it mean to have safe places of work?
- 7 steps to get a bcsp certification even when you’re not living in the USA
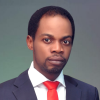
Onyeka Emma is a QHSE Professional with more than 10 years of experience in occupational health and safety, which spans many industries such as construction, beverage, oil and gas, etc. He has many health and safety certifications, including NEBOSH IGC, ISO 9001:2015, ISO 14001:2015, and ISO 45001:2018 Lead auditor certificate. A member of IOSH, ISPON, and Nigeria Red Cross Society. He is interested in business, entrepreneurship, Speaking, and motivating people to do better for themselves. He enjoys leisure with a good motivational book.
I am interested in joining health and safety organization.
Please lynda. Send a mail to info@validworth.com , equally Send in Your CV in that regard
Thank You.
Thanks for the update. Currently done HSE general and 3 with ISPON, Did Fire Fighting with PTI fire Academy and First Aid training with Ispon. Am building my career as I am currently about to take my Second Semester Examination for a PGD in safety Education FUPRE.
But I don’t have a Job and don’t have job experience. After the exams i am interested in finding a Job or internship experience.